在渦北選煤廠皮帶運維體系中,“人機環料”四大關鍵環節一直面臨著諸多挑戰。長達數公里的皮帶廊道,設備運行產生的巨大噪音、灰塵,以及封閉特殊的產線環境等,對傳統人工巡檢模式提出了問題,如何快速定位故障點、早發現早維護?如何確保巡檢人員安全?巡檢效率如何提高……如今,在渦北選煤廠有了破局之法。
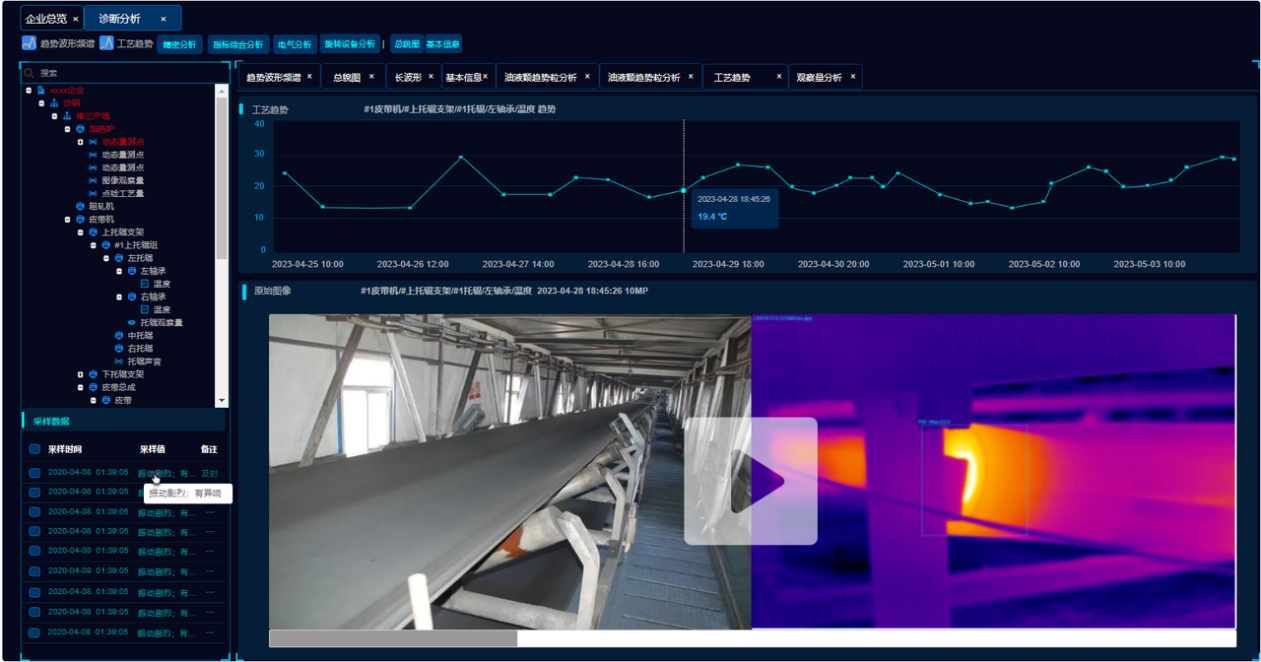
多元感知 感通融合 實現無人化巡檢
該廠原煤、精煤皮帶運輸機通過智能巡檢機器人動態巡檢、定點視頻實時監測、振溫在線監測、皮帶縱撕專項監測多位一體,形成振溫、視頻、圖像、熱像、聲音、氣體等多元化監測。50+AI算法模型部署,部件級故障智能報警,全故障診斷分析,完成周期性皮帶狀態巡檢、關鍵部位24小時監測、異常及時識別和遠程狀態掌控,并通過多種采集設備內部的邊緣智能算法,進行異常狀態聯動控制,可實時監測托輥異常、皮帶跑偏、皮帶撕裂、筒皮變形等關鍵問題,真正實現無人化巡檢。
“當溫度超過40度時,每1小時完成皮帶機仔細巡檢一次,這本來是職工巡檢設備的‘夏季日常’,但最近這項工作交給了這些‘智慧新工友’,讓許多難題迎刃而解”。該廠生產技術部副部長張松山介紹到,“比如,之前在巡檢7001精煤皮帶時,巡檢一次大約30分鐘,環境溫度高,勞動強度大,且存在一定安全風險,如今這些就變得輕而易舉。”
精準監測 排查故障 避免非計劃停車
“‘智慧新工友’的到來真沒讓我們失望,前幾日,2115皮帶棧橋便精準監測到一處橫向裂紋故障,成功避免了一起非計劃停車。”該廠機電車間主任趙翔說。
6月29日周六凌晨兩點多,皮帶機AI智慧監測系統發出報警,2115皮帶出現裂紋損傷,并實時捕捉到損傷位置畫面。監測系統與方案服務商容知日新的診斷專家共同分析,并出具檢維修建議,一致認為皮帶機尚可繼續運行,系統將實時監測裂紋劣化過程,待系統停車后完成故障處理。
7月1日,檢修人員第一時間收到遠程診斷反饋,并迅速啟動復核檢查,最終驗證實際情況與智能系統監測判斷一致,將安排對接頭處進行修補。
新質生產力賦能 實現高質量發展
“目前,全廠有四條皮帶運輸機用上了智能巡檢系統,我們只需動動手指就能完成皮帶巡檢任務,工作更輕松了,效率也更高了。”該廠選煤車間職工代學堂表示。
“我們建成了智控中心及視頻監控系統、管控平臺、3D工廠、5G網絡、智能物流、智能除塵及環監、集控升級、壓風機智能管控系統8個智能化系統,逐步實現了生產、運輸、檢測等崗位智能化的運營管控目標。”該廠選煤副總工程師崔裕濤介紹說。
渦北選煤廠把智能化作為催生新質生產力的有力抓手,進一步厚植發展優勢、應對變革挑戰、贏得發展先機,實現由“點上突破”轉向“面上開花”,從手工操控到程序自控、從徒步巡查到機器巡檢、從現場盯防到遠程管控、從手工分析到智能決策,為智能化選煤廠可持續發展提供強大科技支撐。
(審核:呂剛 責編:尹杰)